Machine Vision Gauging System
|
PTI is offering a new line of fully automatic machine vision gauging systems to
measure precisely critical dimensions of molded precision caps & parts which have to be monitored
during production to keep the mold process under control (temperature, pressure, etc.).
|
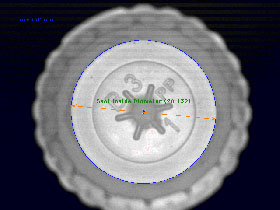 |
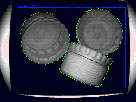 |
All dimensional measurements are completed in less than one minute for a multi-cavity mold and are
ready for computerized statistical process control procedure without operator interface. Operator
error is effectively eliminated. Immediate cost savings are due to reduced operator interface, no operator
|
errors, diminished loss of product due to immediate process control and adjustment in
the production line. Accuracy: +/- 5 microns (0.0002") for parts up to 25 mm (1")
Currently used manually operated optical gauging systems take up to two hours to complete all
measurements. These systems are not fast enough to monitor and adjust a high speed production
process. Potentially this could result in significant losses and lost opportunities due to defective parts.
Manual optical gauging measurements are subjective and very dependent on operator skills and
experience. Even though an optical system is accurate enough, the error due to operator
interpretation makes it unreliable.
|
|
|
VISI-PACK Bottle Neck - Scan Inspection System
|
|
High speed, fully automatic Machine Vision System checks the bottle neck area for
following defects and dimensions:
- Neck Profile
- Neck slant
- Thread profile
- Flash - deformed neck
- Height - T dimension
- Diameter - side view
INSPECTlON CAPABlLITY:
Fully automatic bottle neck inspections system, capable of running a large range of bottle sizes without major mechanical changover.
BENEFITS:
- Fully automatic 100% on-line inspection
- Improves process reliability
- Cost savings - rejects faulty containers before they cause a problem
- Precise and repeatable results
- No operator errors
- No operators required
FEATURES:
- up to 250 bottles per minute
- Integration with Label Inspection System (LIS and LS)
- Integration with Bar Code Reading System
- Integration with other inspection systems
- Automatic detailed diagnostic reports
|
main page |